HIGHLIGHTS
PROGRAM UPDATES
Mass Timber on Verge of Historic Code Breakthrough Wood, Naturally Promotes Wood Benefits at DeckExpo Mass Timber Continues to Overcome Attacks by Concrete WoodWorks: Removing Barriers to Wood Through Audience Diversification Think Wood Keeps Pace With Market Trends AWC Releases New Report on Code Compliance for Sound TransmissionINDUSTRY NEWS
Amazon Invests in Prefab Housing Modular Construction to Hit $157 Billion by 2023 Managed Forests Play Role in Climate Change Mitigation One Mass Timber School Inspires Another Prefab Comes to Passive House The Financial Case for High Performance BuildingsINSIGHTS ON THE COMPETITION
Build With Strength's Marketing CampaignINDUSTRY RESOUCES
Virginia Tech’s Monthly Housing ReportProgram Updates
Mass Timber on Verge of Historic Code Breakthroughs
The proposals will now be subjected to an online government consensus vote, with final results due in mid-December. If approved, the proposals will allow for three new mass timber building types to be constructed in the United States:
Type IV-A – Wood buildings up to 18 stories tall
Type IV-B – Wood buildings up to 12 stories tall
Type IV-C – Wood buildings up to 9 stories tall
Mass timber includes any product currently permitted for use in Type IV construction, such as cross laminated timber (CLT), structural composite lumber, glued-laminated timber, and large section sawn lumber. The SLB estimates that up to 5.1 billion board feet (bbf) of annual demand exists for mass timber construction.
Reflecting on the likely impact, the SLB’s Cees de Jager noted that, “while formal adoption of these code changes won’t take place until well into the next decade, jurisdictions have the opportunity to incorporate the tall wood building provisions into their current code.” He noted that Oregon recently approved an addendum to its building code that allows timber structures to be built over six stories without having to acquire special permission. Code changes are seen as a turnkey intervention that will encourage more developers and architects to design projects in wood from the start, versus attempting to convert from steel or concrete to wood later in the process.
The SLB joins the industry in eagerly awaiting the outcome of the online vote and is committed to capturing the market share opportunities created by code changes.
nline vote and is committed to capturing the market share opportunities created by code changes.
Wood, Naturally Promotes Wood Benefits at DeckExpo
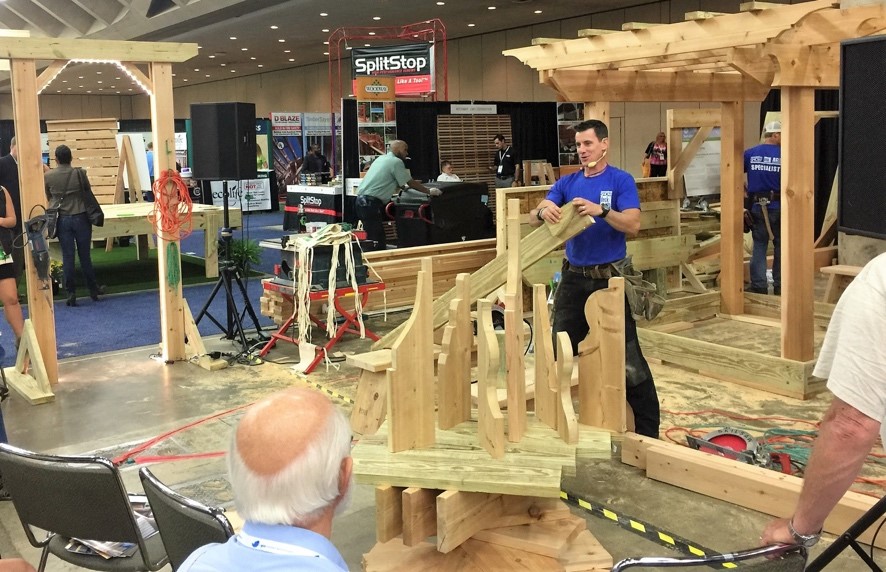
Wood, Naturally recently teamed with three partner associations—the Southern Forest Product Association (SFPA), the Western Red Cedar Lumber Association, and the Southeastern Lumber Manufacturers Association—to promote the benefits of wood at the annual DeckExpo trade show, held in October in Baltimore. This is the second consecutive year that Wood, Naturally exhibited at this trades-only show, which attracts more than 5,000 design and build professionals annually.
Wood, Naturally’s 20×20 exhibit featured handcrafted projects constructed using pressure-treated southern pine and western red cedar, including a bulkhead/retaining wall, a privacy fence, a raised deck, a Japanese-style torii gate, and a pergola. The projects highlighted wood’s versatility and beauty in outdoor settings. The exhibit also hosted six demonstrations by carpentry expert Mark Clement to standing-room-only crowds and had on hand industry publications that offered additional outdoor building ideas and construction tips.
Mass Timber Continues to Overcome Attacks by Concrete
A recent op-ed published by the Mass Timber Building Coalition takes aim at the misleading claims of the concrete industry as it attempts to discredit the code compliance and performance qualities of mass timber despite a preponderance of evidence to the contrary. Concrete has gone so far as to suggest that the International Code Council (ICC) process for considering proposals is itself misguided.
In doing so, the concrete industry seeks to undermine the fact that the purpose of the International Building Code (IBC) is to provide code officials with the tools they need to ensure safety in the built environment, irrespective of the market position of any material or industry—including softwood lumber. Rather, the ICC code development process as applied to tall mass timber buildings and any other building system is predicated on science. In tall wood’s case, an ICC-appointed Ad Hoc Committee on Tall Wood Buildings undertook two years of research, including full-scale fire-resistance testing at a federal fire lab, to fully understand the science of mass timber and recommend code changes to ensure safety.
This rigorous process may not sit well with certain industry groups, but the public will be safer as a result while benefiting from the clear environmental and economic advantages of mass timber buildings.
WoodWorks: Removing Barriers to Wood Through Audience Diversification
For mid-rise projects especially, WoodWorks has observed more and more developers and contractors getting involved in structural material decisions alongside building design teams. Often these individuals have long histories of using steel or concrete, and lack both practical experience with and/or confidence in wood as a viable and potentially better choice for their projects.
To overcome this barrier, WoodWorks is going to new places and events to reach and build relationships with this new segment of its audience. In recent months, WoodWorks participated in one-on-one developer meetings during the MultiFamily Executive Conference, met with contractor associations and firms to discuss education needs related to mass timber installation, and started attending developer- and contractor-focused events run by organizations such as the Urban Land Institute and the Commercial Real Estate Development Association.
Think Wood Keeps Pace With Market Trends
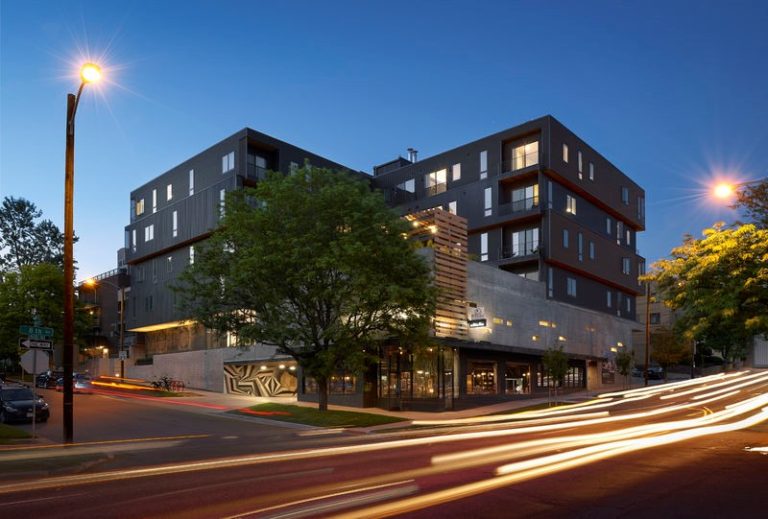
Big names like Amazon and Google are joining boutique firms like Katerra in rapidly entering the building sector as they realize the efficiencies and potential profitability of prefabrication and off-site construction. Both prefab and off-site construction have seen exponential growth in recent years as a nationwide construction labor shortage forces builders and developers to leverage process efficiencies at every stage of construction.
Prefabricated wood building systems in particular—which are no longer limited to single-family homes and small, temporary workspaces—have a unique value proposition with many benefits, including high quality control standards, material efficiency, reduced waste, safer working environments, and outstanding return on investment.
Think Wood is ensuring that the benefits of prefabricated wood building systems are continuously communicated to architects, engineers, and developers by
- Curating the latest high-impact research on prefabricated wood building systems.
- Educating architects and engineers on wood prefabrication.
- Highlighting thought leaders who are rapidly adopting and investing in softwood lumber technology and construction.
- Leading the narrative about wood’s advantages in prefabrication.
AWC Releases New Report on Code Compliance for Sound Transmission
The AWC has released a new report on sound transmission, Technical Report 15 (TR15), Calculation of Sound Transmission Parameters for Wood-Framed Assemblies, to support building professionals in meeting stringent code requirements regarding sound in wood buildings.
TR15 describes how acoustics for floor-ceiling assemblies are regulated in the code and provides a code-recognized, calculation-based model that can be used to demonstrate compliance for wood-framed floor-ceiling assemblies. The acoustics model can also be used to quickly determine the effect of changes to basic assemblies or proprietary designs without needing to undertake further engineering analysis or costly physical testing of each new variation.
A free PDF version of TR15 can be found here. The AWC also developed a companion, ICC-accredited, free e-course that provides an understanding of the calculation-based analysis approach, which is available here.
Industry News
Amazon Invests in Prefab Housing
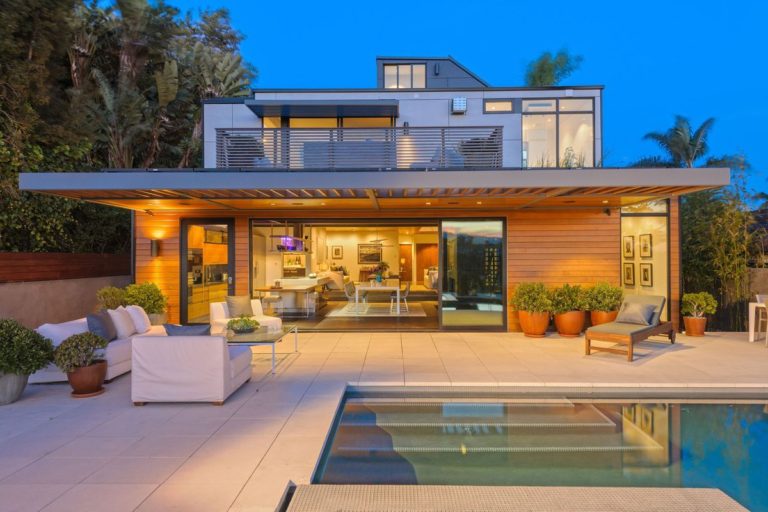
Technology giant Amazon has moved into prefabricated construction by investing in home-building start-up Plant PreFab, based in Rialto, Calif. Plant PreFab is well-known for smart home technology and sustainable construction and is set to become the latest addition in Amazon’s Alexa-integrated homes. Amazon’s Alexa Fund invested in Plant PreFab for prefabricated single-family and multifamily houses and for a plan to use automation to build homes faster and at lower costs.
Modular Construction to Hit $157 Billion by 2023
A recent study by MarketsandMarkets™ suggests that the worldwide value of the modular construction market will hit $157.19 billion by 2023. Cost appears to be a key driver in modular construction’s growth as both builders and buyers realize significant savings. Prefabricated modules mean less labor and less time spent building on site, which allows for construction of buildings in shorter time frames, resulting in lower costs all around.
In the United States, start-ups like Factory_OS and Katerra in California, Kasita in Austin, Texas, and Blokable in Seattle, Wash., are finding success offering modular construction solutions to solve affordable housing shortages. Meanwhile, Google has built massive data centers out of refurbished shipping containers all around the world, and Marriott and Starbucks are among the other blue-chip companies embracing prefabrication in their corporate efforts.
Managed Forests Play Role in Climate Change Mitigation
The Intergovernmental Panel on Climate Change believes that some degree of afforestation will be needed to limit global warming and temperature rise. Afforestation occurs when new forests are planted across land without trees, be it as natural forests, commercial plantations like timber farms, or agroforestry sites. In all cases, as a forest grows, it naturally removes CO2 from the atmosphere and stores it in its trees. In the case of timber plantations, which tend to be harvested every decade or so, if the harvested wood is used in building construction, it will retain most of its carbon without releasing it back into the atmosphere.
Thus, forests that support building construction in the United States and around the globe, when well and appropriately managed and harvested, can have an increasing role to play in mitigating climatic change.
One Mass Timber School Inspires Another
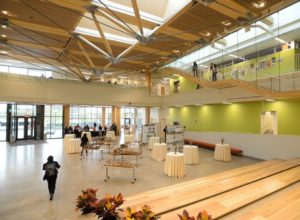
The School Building Advisory Committee in Holyoke, Mass., is exploring using CLT as structural and design material in two proposed middle schools in its district. The committee and project architect found inspiration in the nearby four-story, 87,500-square-foot John W. Olver Design Building at the University of Massachusetts, Amherst, which incorporates innovative wood systems including CLT. The Holyoke committee members and a structural engineer recently visited the Olver Design Building to get an up-close look.
The committee and design team are drawn to CLT as it is more environmentally responsible than other material options, aesthetically pleasing, and faster to construct.
Prefab Comes to Passive House
Prefab builder Bensonwood recently launched PHlex, a prefabricated wall panel for use in Passive House buildings, which builders can buy and use to assemble custom homes on site. PHlex meets Passive House’s standard for air tightness by customizing walls for clients in terms of length, height, and thickness. This allows a PHlex system to adapt to an individual building’s parameters to achieve Passive House performance, including the local climate, the orientation of the home, occupancy, square footage, and budget.
The Financial Case for High Performance Buildings
A California-based real estate services firm, stok, recently published a report on the role that high-performance buildings (HPBs) can play in improving employee health and wellness, including via the benefit of being connected to the environment through generous amounts of daylight and the use of natural materials such as wood.
Stok applied financial impact calculations to findings from more than 60 research studies on the effect of HPBs on employee productivity, retention, and wellness. It found that while utility and maintenance cost savings are the most frequently cited benefits of HPBs, they offer some of the smallest financial value. Instead, 43% of the total value comes from enhanced employee productivity, 41% from increased employee retention, 7% from improved employee wellness, 7% from utility savings, and 2% from maintenance savings.
Insights on the Competition
Build With Strength's Marketing Campaign
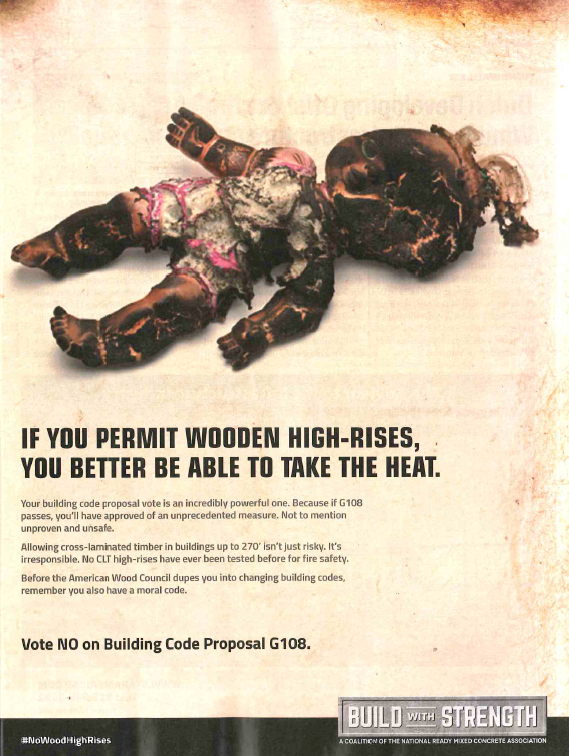
In the lead-up to the ICC Public Comment Hearings in Richmond, Va., in late October, concrete’s Build With Strength campaign continued to assail mass timber and the two years’ worth of research that proves its viability as a structural material in tall buildings. Concrete’s latest print ad, which appeared in the 2018 Fall issue of ENR Magazine, used particularly extreme imagery and language to depict wood as unsafe.
Despite Build With Strength’s negative marketing and the nearly 250 public comments the concrete and steel industries mobilized in opposition, science and reason prevailed. The ICC’s membership approved all 14 tall wood building proposals put forward by the Ad Hoc Committee on Tall Wood Buildings during the hearings in Richmond, with each tall wood proposal advancing with majority votes of at least 68%. The 14 proposals will now be subject to two weeks of online voting, resulting in a final action in December.
Although the SLB expects that concrete and steel will continue to be competitive threats to wood (and willing to engage in fairly unscrupulous communications tactics to elevate their own products), we are confident that wood’s performance history will serve as the best response to their claims.
Industry Resources
Virginia Tech’s Monthly Housing Report
This monthly housing commentary report is a free service of Virginia Tech and is intended to help one gauge future business activity in the U.S. housing market.
August 2018 Reports (Released in October)
- Part A: August Housing Commentary
- Part B: August Economic Conditions