HIGHLIGHTS
PROGRAM UPDATES
ICC 2021 Standards Update – Beyond Mass Timber Timber on the Rise: Influencing Wood Use for Architects, Builders, and DevelopersINDUSTRY NEWS
CLT Manufacturer Helps Preserve Local Timber Industry NY Times Article Features Advances and Benefits of Wooden High-Rise Construction Economist Article Examines Wood as the Solution to the Green Building Problem Course Looks to Train the Next Generation of Mass Timber Builders 2019 California Mass Timber Building Competition Seeking Entrants View the T3 Atlanta Building’s Drone Construction Footage Off-Site Practices are on the RiseINSIGHTS ON THE COMPETITION
Remind Your Customers – Concrete is Responsible for 8% of Worldwide CO2 EmissionsINDUSTRY RESOUCES
Virginia Tech’s Monthly Housing ReportProgram Updates
ICC 2021 Standards Update – Beyond Mass Timber
In addition to the historic proposals allowing mass timber buildings up to 18 stories tall, recent International Code Council (ICC) online voting also confirmed over 350 other proposals for inclusion in the ICC 2021 standards. Several of these were developed and championed by the American Wood Council (AWC) on behalf of the softwood lumber industry. For example, new changes will allow continued use of forced air for dust control in lumber mills, clarify protection required for exterior wall/floor intersections in wood-frame platform construction, permit heavy timber elements to be used in exterior walls, and allow concealed spaces in heavy timber (Type IV) buildings.
Importantly, the AWC’s outreach helped to defeat several proposals that would have interfered with wood’s market share, including proposals that sought to require that interior and exterior surfaces of lightweight wood framing be protected by drywall continually during construction and to create criteria for fire testing of wood siding while allowing insulated vinyl siding to go untested.
Timber on the Rise: Influencing Wood Use for Architects, Builders, and Developers
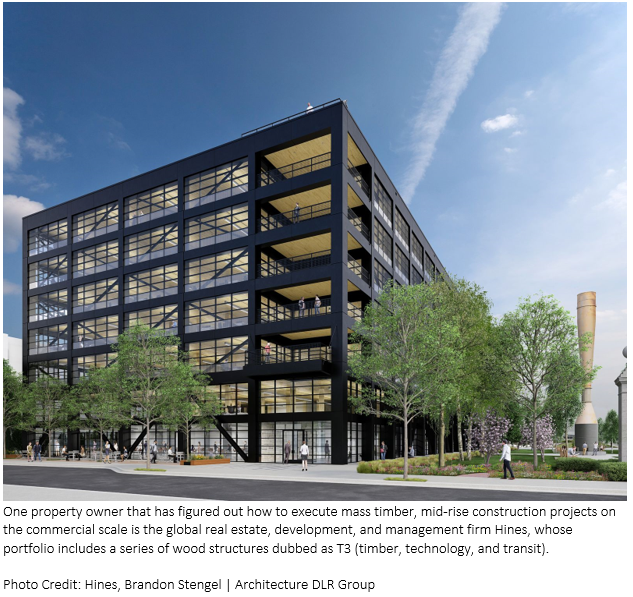
Recent industry research asserts that technical experts, academics, and peers are the top three most credible voices when it comes to influencing decision-making in building material specification. For Think Wood, leveraging the voices of industry experts along with top architects, builders, and developers is critical in communicating the value proposition of wood and positioning it as the go-to building material in North America.
Over the past year, Think Wood has teamed with Architect magazine’s ArchitectChat podcast and its “Timber on the Rise” series to amplify the voices of experts who share their stories and experiences about innovating and building with wood as a primary building material.
Click a link to listen:
- Behind the Scenes at Hampshire College’s R.W. Kern Center—The role of wood in a net-zero building
- Katerra Tackles the Inefficiencies of the Building Industry—And why it is heavily investing in mass timber R+D and production
- How to Design Commercially Viable Mass Timber Buildings—Learnings from Hines and DLR Group
- The Case for Designing with Nail-Laminated Timber
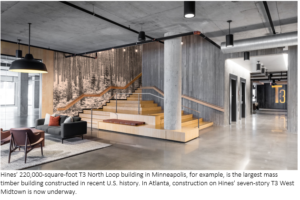
Industry News
CLT Manufacturer Helps Preserve Local Timber Industry
Timber has long been king in parts of northwestern Montana, and it looks to stay that way thanks in part to the arrival of SmartLam, the first manufacturer of cross-laminated timber (CLT) products in the United States. SmartLam launched operations in a 40,000-square-foot manufacturing facility in Flathead County, Mont., in 2012, with an annual production capacity of over 28,000 cubic meters of CLT. Because of strong demand, SmartLam recently expanded its operations to a nearby former Weyerhaeuser mill.
SmartLam’s growth means growth for local producers and mills, like F.H. Stoltze Land & Lumber Co., which has seen its production rise over 27% from 2016 to 2018 and has grown its workforce by 18% over the same period. Recent building code revisions and growing awareness of the benefits of CLT are expected to herald even more growth in the coming years.
NY Times Article Features Advances and Benefits of Wooden High-Rise Construction
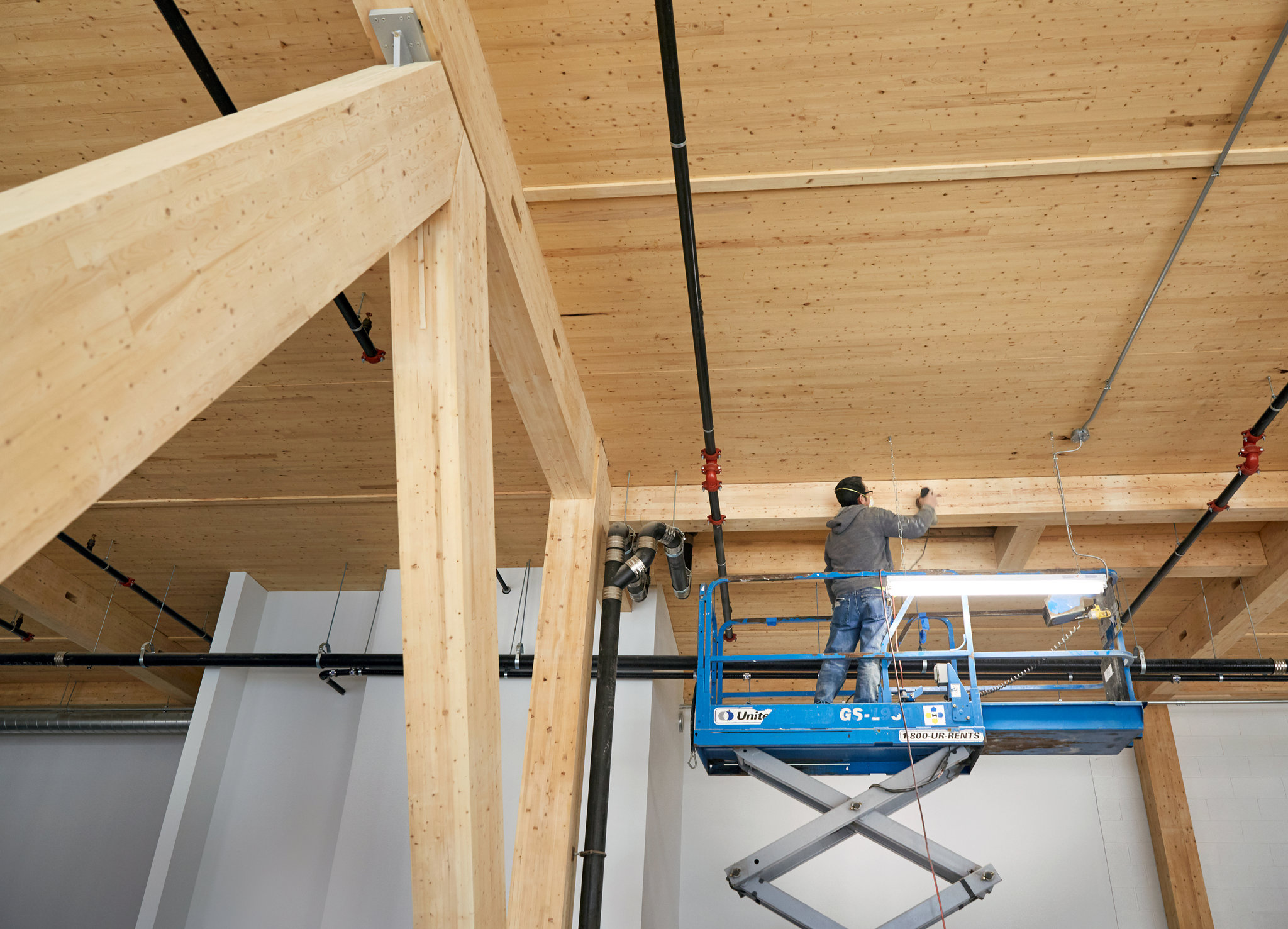
Increasingly motivated by a desire for sustainability, consumers are playing an important part in prompting more builders to explore mass timber for new office, apartment, and institutional buildings. Of the crop of tall mass timber buildings already erected in the United States, their beautiful designs, energy efficiency, and copious amenities are helping to win more fans as these buildings debunk long-held negative stereotypes about what it is like to live and work in wood buildings.
Challenges still remain, though, as permitting often proves cumbersome because of existing height limits for wood buildings and because mass timber buildings sometimes cost more than their concrete and steel peers. Both of these challenges will lessen as the use of mass timber in taller buildings grows. Ben Kaiser, the developer behind the eight-story Carbon12 condominium project in Portland, Ore., summed it up by saying: “It’s like anything—the first iPhone, the first flat-screen TV… costs are high because not enough people are doing it.”
Economist Article Examines Wood as the Solution to the Green Building Problem
Recent analysis by The Economist concluded that ongoing efforts to make buildings greener and cut carbon emissions are not working. Many zero-carbon buildings neither perform as efficiently nor generate as much renewable energy as expected; meanwhile, incentive programs are undersubscribed and not creating the benefits at scale as promised.
The authors cite taxes as one possible, durable solution to force greener buildings, but note taxes are both unpopular and likely to be disproportionally felt by poor people, who do not have the money to upgrade windows, insulation, and so on. Instead, they settle on a more likely solution: more buildings should be made of wood. They note that producing a laminated wood beam takes only one-sixth of the energy needed for a steel beam of comparable strength; trees take carbon out of the atmosphere when growing, and wooden buildings contribute to negative emissions by storing carbon. In the writers’ words, “No other building material has environmental credentials as exciting and overlooked as wood.”
Course Looks to Train the Next Generation of Mass Timber Builders
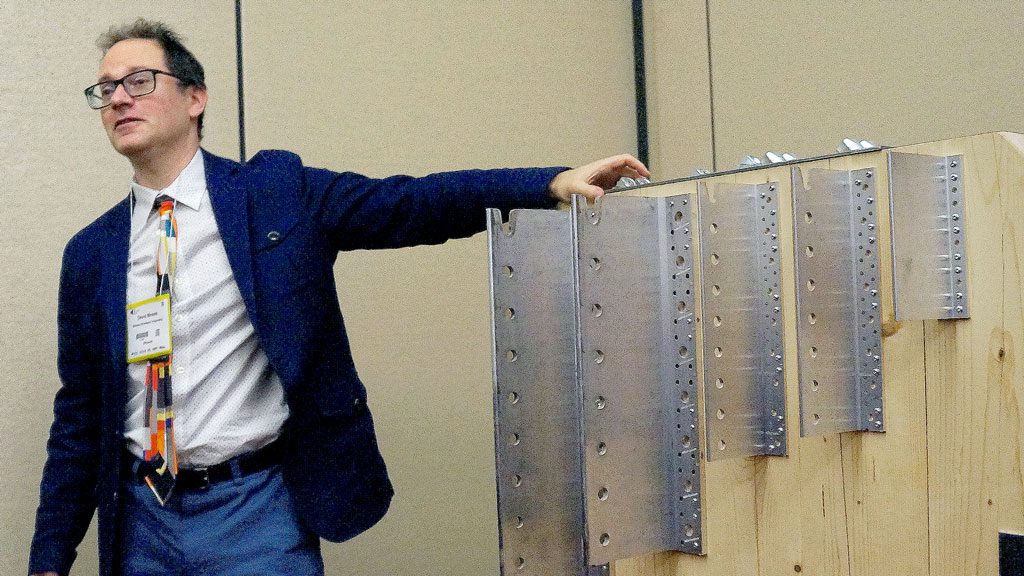
As more architects and designers are inspired to use mass timber in their projects, there is a growing need to educate professionals in the construction sector on how to build with it. Moses Structural Engineers in Toronto is currently working with Ontario’s Ministry of Natural Resources and Forestry, Carpenters’ Local 27, and the College of Carpenters and Allied Trades (CCAT) in Vaughan, Ontario, to develop several mass timber modules that can be built and disassembled by apprentices and carpenters. The modules will be the basis of a four-week training course launching in March at the CCAT.
2019 California Mass Timber Building Competition Seeking Entrants
The California Government Operations Agency (GovOps), with support from the Binational Softwood Lumber Council, will award $500,000 in grants as part of the statewide California Mass Timber Building Competition, hosted by GovOps and administered by WoodWorks. Grants will be awarded to selected proponent teams presenting viable and repeatable mass timber solutions for commercial and multi-family projects in California. The deadline for submissions is March 18, 2019.
View the T3 Atlanta Building’s Drone Construction Footage
StructureCraft is using drones to help building lovers keep pace with the construction of Hines’ seven-story, 200,000-square-foot T3 Atlanta office project. Once built, T3 Atlanta will assume the title of the largest mass timber building in the United States. T3 Atlanta shares its design with its predecessors, the original T3 building in Minneapolis and T3 Chicago, which is currently under construction. All of Hines’ T3 buildings are constructed using nail-laminated timber, and replicating the proven design offers the added benefit of increased cost-efficiency. Learn more at structurecraft.com/projects/t3-atlanta.
Off-Site Practices are on the Rise
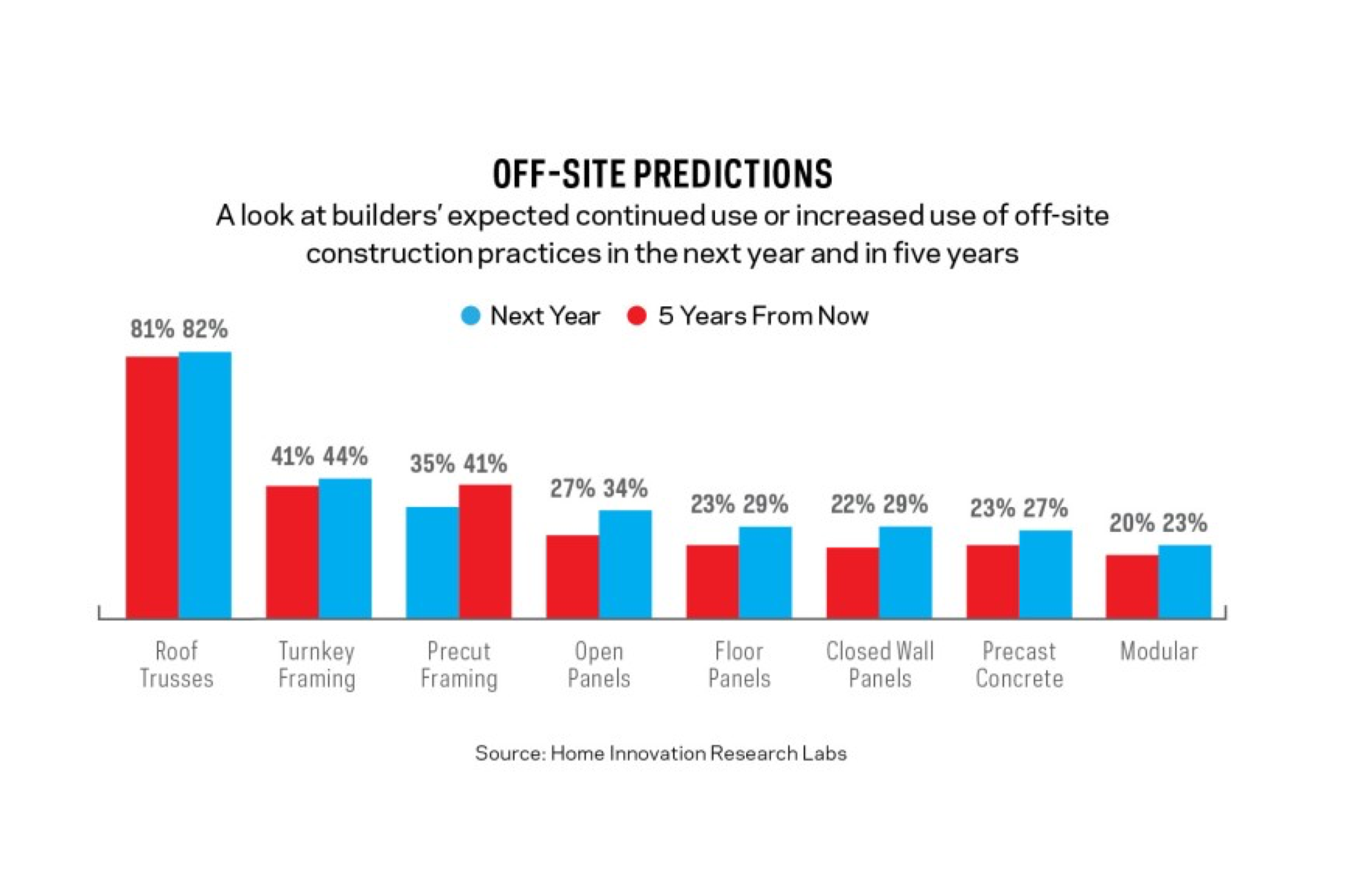
A recent Home Innovation survey reveals the pace of transition from on-site to off-site construction is picking up. Competition among various off-site housing solutions will not likely be “winner take all.” Rather, it looks like several different solutions have their own followings and will be able to grow.
In April, Home Innovation conducted a survey of 300 U.S. homebuilders. Home Innovation included seven off-site construction practices and asked builders about their anticipated use of each in the coming year. The survey was repeated in December to gauge change in builder sentiment; Home Innovation also included a new question to gauge builders’ anticipated use of off-site systems in five years.
Insights on the Competition
Remind Your Customers – Concrete is Responsible for 8% of Worldwide CO2 Emissions
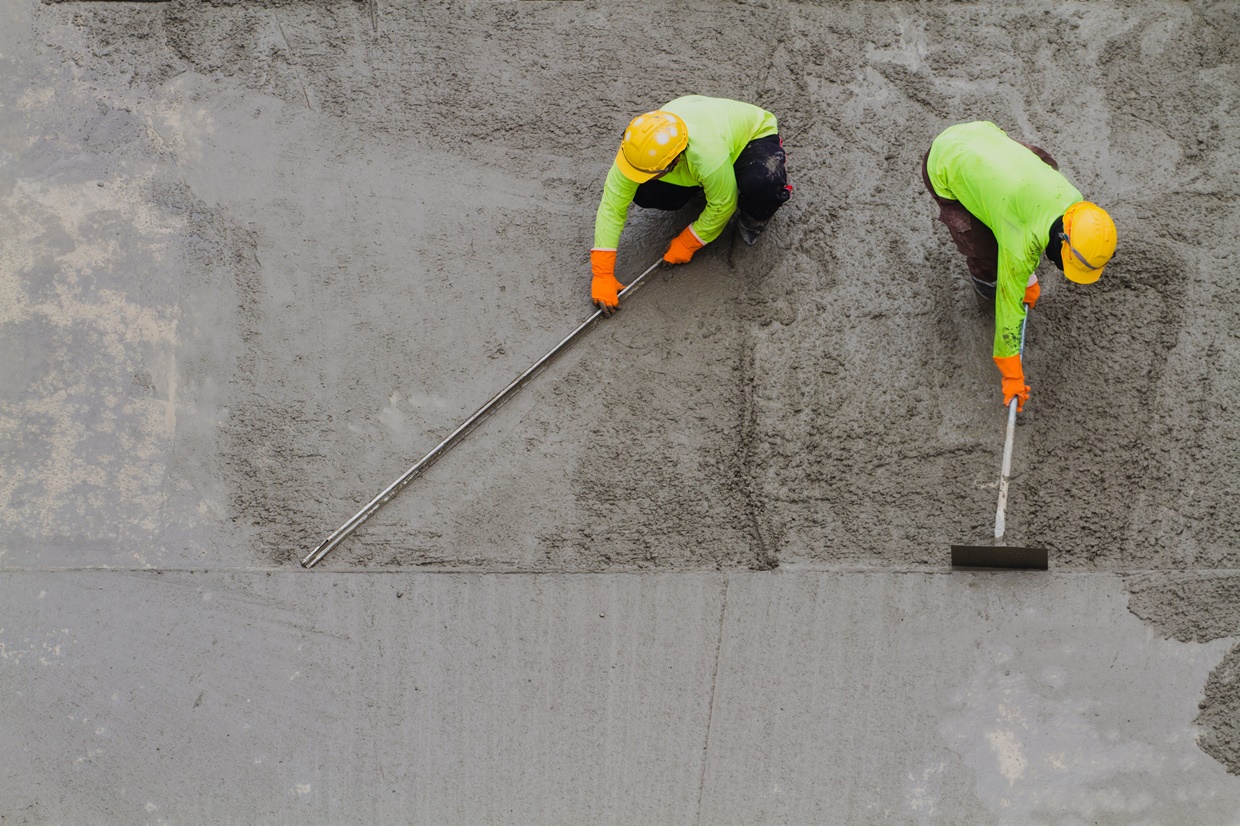
New research by the influential UK-based think tank Chatham House underlines the need for drastic changes in the production and use of concrete. Concrete is the world’s most used man-made material and alone is responsible for 8% of the world’s CO2 emissions. Anthony Thisleton and Simon Sturgis go so far as to urge architects and engineers to reconsider their use of concrete and find more environmentally friendly alternatives such as wood, which can offer the same strength and performance qualify in a host of applications.
Industry Resources
Virginia Tech’s Monthly Housing Report
This monthly housing commentary report is a free service of Virginia Tech and is intended to help one gauge future business activity in the U.S. housing market. Due to the government shutdown, the Virginia Tech Housing Report has not been updated. We expect updates to resume next month.