HIGHLIGHTS
PROGRAM UPDATES
AWC: Tall Mass Timber Code Changes Get Final Approval Think Wood and Wood, Naturally Combine to Target Commercial and Residential Construction WoodWorks: Innovative Partnerships Expand Messaging Reach Think Wood Drives Momentum for Wood at National EventsINDUSTRY NEWS
Trends to Track Robotics Arrive in U.S. Construction The Pros and Cons of Prefabricated Construction University Finds Solution in Wood-Based Modular HousingINSIGHTS ON THE COMPETITION
N.J. Anti-Wood Construction Bill Changes as Result of HearingProgram Updates
AWC: Tall Mass Timber Code Changes Get Final Approval
The International Code Council (ICC) has released the unofficial voting results on code change proposals considered in 2018, including passage of the entire package of 14 tall mass timber code change proposals. The proposals create three new types of construction (Types IV-A, IV-B, and IV-C), which set fire-safety requirements as well as allowable heights, areas, and number of stories for tall mass timber buildings. Official results are expected to be announced during the first quarter of 2019. The new provisions will be included in the 2021 International Building Code (IBC).
“Mass timber has been capturing the imagination of architects and developers, and the ICC result means they can now turn sketches into reality. ICC’s rigorous study, testing, and voting process now recognizes a strong, low-carbon alternative to traditional tall building materials used by the building and construction industry,” said American Wood Council (AWC) President and CEO Robert Glowinski.
This outcome represents in part the efforts of the Softwood Lumber Board (SLB), which alongside the AWC and the U.S. Endowment for Forestry and Communities, funded a multiyear initiative led by AWC to generate new data to demonstrate the performance of tall mass timber structures, engage and educate code and fire officials, and ultimately gain acceptance for tall wood in building codes and standards.
Think Wood and Wood, Naturally Combine to Target Commercial and Residential Construction
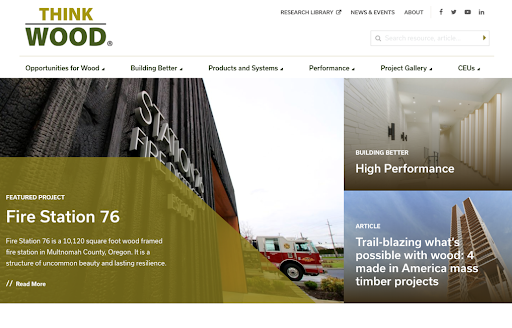
As a result of the consolidation, the Think Wood program will be focusing its marketing and communication efforts in 2019 on architects, engineers, developers, and contractors. The account team responsible for executing Wood, Naturally activities will be a key partner for the Think Wood program, providing marketing strategy recommendations and execution for paid, earned, and owned media channels.
WoodWorks: Innovative Partnerships Expand Messaging Reach
WoodWorks is successful thanks in large part to its staff of specialists who provide credible, expert support to building design professionals. WoodWorks has earned and continues to grow its reputation as the “go to” technical resource for wood applications, and new, innovative partnerships are enabling it to expand its reach even further.
For example, the California Government Operations Agency (GovOps) recently announced that it will award $500,000 in grants to design/developer teams as part of a statewide Mass Timber Building Competition. WoodWorks worked closely with GovOps to develop the competition and will serve as its administrator thanks to funding from the Binational Softwood Lumber Council. Because WoodWorks will not judge entries, it can provide its expert project support to interested teams.
Meanwhile in Seattle, a developer/design team chose to use softwood lumber instead of steel or concrete for a 12-story project thanks to WoodWorks’ technical support. The team was struck by the paucity of public information on certain aspects of mass timber building design and so decided to create a book based on their design and construction process. At the developer’s invitation, WoodWorks co-developed the book’s forward and contributed a chapter on the state of the mass timber industry.
Think Wood Drives Momentum for Wood at National Events
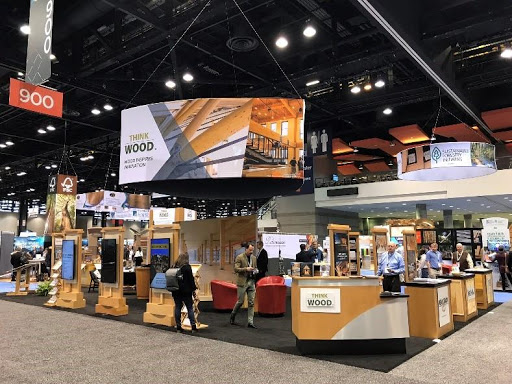
SLB and industry research shows that attending trade shows and in-person events is an important way for developers, architects, and engineers to learn about the benefits of wood construction. Think Wood works on behalf of the industry to create a unified, coordinated presence at shows and spur conversations about the economic, environmental, and societal benefits of softwood and next-generation lumber products and systems.
Think Wood recently coordinated a presence at two large national events, the Innovations Conference in New York and Greenbuild in Chicago. At the Innovations Conference, Think Wood observed unprecedented levels of interest thanks in part to its sponsored speakers, Tanya Luthi of Fast + Epp and Marc Rivard of WoodWorks, as well as others who spoke about the benefits of wood construction. The interest levels at the conference are indicative of growing demand nationwide for more information about innovative wood building systems. Following the talks, WoodWorks, too, received a high volume of questions and requests for follow-up support.
Meanwhile at Greenbuild, there was a surge in detail-oriented questions and engagements, mostly focused on “how to build with wood,” rather than “is it even possible to build with wood?”
Industry News
Trends to Track
Analysts at ProSales named key trends to watch related to construction, demographics, environment, logistics, and technology that will shape construction and lumber manufacturing over the next 30 years. ProSales highlighted the pending ICC code changes related to tall wood buildings as ready to yield rapid and widespread growth in mass timber. They are less certain of the impact of 3-D printing, which speeds up construction but is not accepted by code and has not been around long enough to ensure durability. There has been limited testing of 3-D printing with wood while concrete and other materials are widely used.
ProSales is part of a chorus of analysts that expect the United States’ increasingly aging population to herald in many design changes in housing and predict a rise in shared and multigenerational housing. ProSales also expects a shift to more offsite construction and an increased emphasis on resilience because of increased frequency and intensity of natural disasters.
Robotics Arrive in U.S. Construction
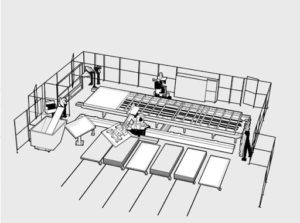
Scandinavian firms have been at the forefront of developing robotics able to produce framed buildings. This technology is now coming to the United States as California-based modular construction company Katerra recently purchased three ZeroLabor units from Swedish company Randek, to be delivered this spring. Comparable robotics systems have been able to quintuple productivity without any increase in staffing.
Robots have yet to make a significant dent in the production homebuilding industry, but industry watchers predict that the crisis-level shortage of skilled labor in the United States could be what tips builders toward automation. Machines now carry out 29% of all workplace tasks, and that is expected to hit 52% by 2025, according to a recent World Economic Forum report.
The Pros and Cons of Prefabricated Construction
The United States is seeing a resurgence of prefabricated construction, fueled by an abundance of technology and a shortage of labor. Prefabricated construction almost universally offers greater consistency, precision, quality control, and efficiency as builders avoid issues related to weather and job site logistics and can improve planning.
A growing number of case studies in the United States, particularly out of California, hint that this could be a favorable and lucrative shift for the wood products industry, as already over $1.1 billion of investment funding has been raised to roll out prefabricated home and multifamily, student, and assisted-living facility factories across the United States. Examples from elsewhere in the world show what the shift may look like. For example, at Japan’s Sekisui House, the world’s largest residential builder, one campus designs, develops, and produces more than 470 buildings a month. As many as 600 trucks loaded with construction components roll out of Sekisui House’s complex daily.
However, the shift may not prove equally positive for all segments of the softwood lumber industry. Lumberyards in particular may face new threats to their businesses, as prefabricated construction factories opt to buy directly from mills, reduce their orders as less material waste equates to reduced overall need for materials, or do both. Lumber mills may face their own challenges as prefabricated construction factories will demand framing wood with less warp, wane, and bark. Mills will have to consistently produce better quality studs than what they commonly ship out today.
University Finds Solution in Wood-Based Modular Housing
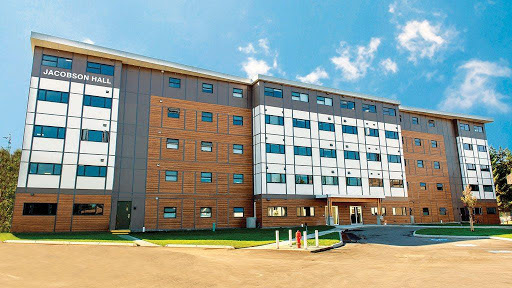
Long waiting lists for student housing and skyrocketing demand in crowded and expensive rental markets led Canada’s Trinity Western University to turn to an innovative solution: wood-based modular housing. Working with Metric Modular, a British Columbia–based modular builder, the university was able to newly accommodate 220 students following the construction of a five-story residence hall in only nine months. The building includes dorm rooms, common areas, and all the other amenities of a traditionally built residence hall, but was constructed more quickly and for a fraction of the cost. The university is also proud to access inherent sustainability benefits offered by wood construction, including a lighter carbon footprint than other commonly used building materials.
When universities need more beds and quickly, wood-based modular housing is an ideal solution.
Insights on the Competition
N.J. Anti-Wood Construction Bill Changes as Result of Hearing
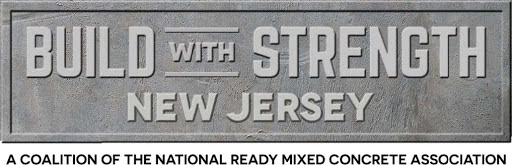
The concrete industry’s Build With Strength campaign is intensifying its efforts to pass anti-wood legislation in New Jersey. Build With Strength is growing a coalition of allies voicing opposition to wood in New Jersey and working to pass county-level legislation in an effort to demonstrate popular support for their position en route to state-level legislation. If passed, state legislation will limit the use of softwood lumber in new mid- and high-rise lightweight construction. American Wood Council will continue to monitor the situation and respond appropriately.
Industry Resources
FEA’s Housing Dashboard
This housing dashboard is provided compliments of Forest Economic Advisors (FEA).
Virginia Tech’s Monthly Housing Report
This monthly housing commentary report is a free service of Virginia Tech and is intended to help one gauge future business activity in the U.S. housing market.
October 2018 Reports (released in December)
Part A: October Housing Commentary
Part B: October Economic Conditions