HIGHLIGHTS
PROGRAM UPDATES
The AWC Participates in ICC Hearings and Expo ANSI Approves 2022 Fire Design Specification Think Wood’s Media Partnerships Reached More Than 1,000 New Building Professionals in Q3 WoodWorks Lays Groundwork for Sound LCA PracticesINDUSTRY NEWS
Maine’s First Mass Timber Office Building Will Promote CLT Adoption Why Increased Focus on Embodied Emissions is an ‘Ironclad Rule of Carbon’ ‘Architecture at Home’ Exhibit Has Five Prototype Homes That Show Housing Can Be ‘Sustainable and Attainable’ Massachusetts Mass Timber Project Targets Passive House Standards The Disappearing Starter Home—and What Might Replace ItINSIGHTS ON THE COMPETITION
Hydrogen-Fueled Production Could Decarbonize the Steel IndustryProgram Updates
The AWC Participates in ICC Hearings and Expo
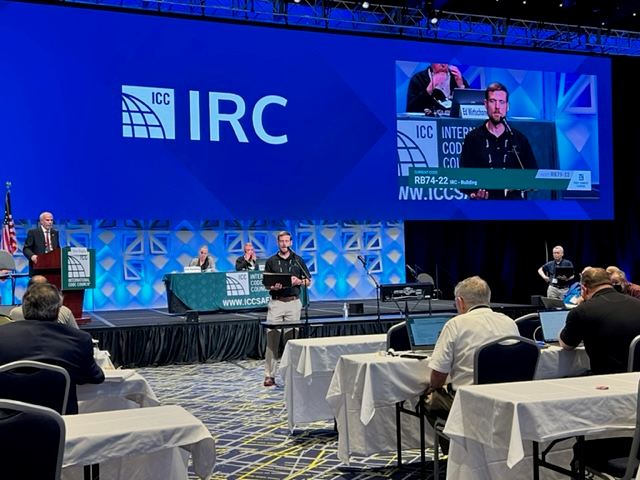
The International Code Council (ICC) Public Comment Hearings for development of 2024 I-Codes concluded in late September, after four days in Louisville, Kentucky. Altogether, the committee considered 350 public comments on 235 code changes to the Administrative Provisions, International Building Code (Structural), International Residential Code (Building), and International Existing Building Code. The AWC was present for the hearings and interacted directly with attendees on the exhibition floor against the backdrop of the Think Wood Mobile Tour.
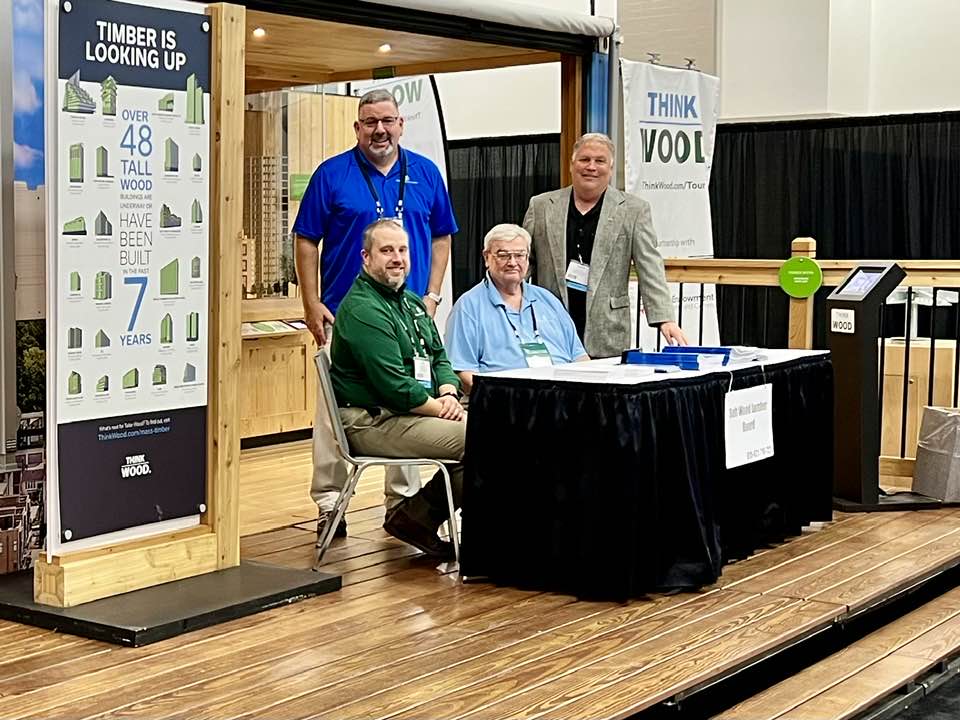
Several positive code changes of importance to the wood industry received no public comment and moved to the consent agenda with favorable committee recommendations. The AWC expects final passage of these changes, which include updating industry design standards, product standards, and coordinating code language for their use in the design of wood structures.
However, some code changes relevant to the wood industry did receive public comment:
• ADM6: This change would have required any burned structures outside the Wildland Urban Interface zone to be rebuilt to the international Wildland Urban Interface Code, bypassing established mapping processes. Action: Disapproved, Favorable Industry Outcome.
• S178: This was an attempt to introduce embodied carbon criteria into the International Building Code for several primary building materials, including wood, by requiring environmental product declarations for 75% of wood products and members based on cost. The AWC opposed the change on the basis that the building code is not the place to regulate embodied carbon. Action: Disapproved, Favorable Industry Outcome.
• RB176: Without the modifications provided by the AWC’s public comment, exterior wood deck structural elements such as guards, deck boards, stair treads, and stringers would be excluded from existing requirements to be preservative-treated or naturally durable wood to protect against decay. Action: Approved as Modified by Public Comment 1, Favorable Industry Outcome.
• RB193, RB195, and RB239: These changes add simplified fastening options for roof, wall, and soffit wood structural panel sheathing attachments to wood frame into the International Residential Code. The changes allow a prescriptive option that avoids engineered design, thereby saving cost, when low specific gravity framing is used. Action: Approved as Modified by Public Comment 1, Favorable Industry Outcome.
ICC validated voters will have the opportunity to take final action on several changes through online voting in October. Final decisions on code-change proposals to be included in the 2024 I-codes are expected in January 2023.
ANSI Approves 2022 Fire Design Specification
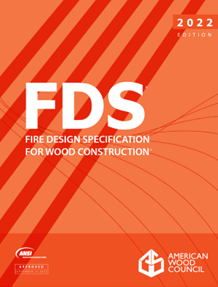
The AWC has received ANSI approval of its Fire Design Specification for Wood Construction (FDS) as an American National Standard—a significant accomplishment given the importance of managing fire risk for wood construction in the building codes. The approved FDS consolidates all relevant provisions into one standard that is managed by the AWC under an ANSI consensus process.
The new standard, designated as ANSI/AWC FDS-2022, is a comprehensive, consensus-based resource that brings together all the provisions for the fire design of wood members, assemblies, and connections to meet code requirements. The FDS is the authoritative standard for use by architects, engineers, building and fire officials, and other professionals that need code-compliant solutions for wood and mass timber construction.
The AWC will seek to have the FDS referenced in future building codes, which would eliminate the need to have technical discussions on code provisions related to wood and fire risk during the ICC code hearing process. Instead, technical issues would be managed through an ANSI review process at a cadence that the AWC prefers. The ANSI process also ensures decisions are reached through consensus and in a setting that allows the AWC greater ability to discuss and resolve technical issues.
Think Wood’s Media Partnerships Reached More Than 1,000 New Building Professionals in Q3
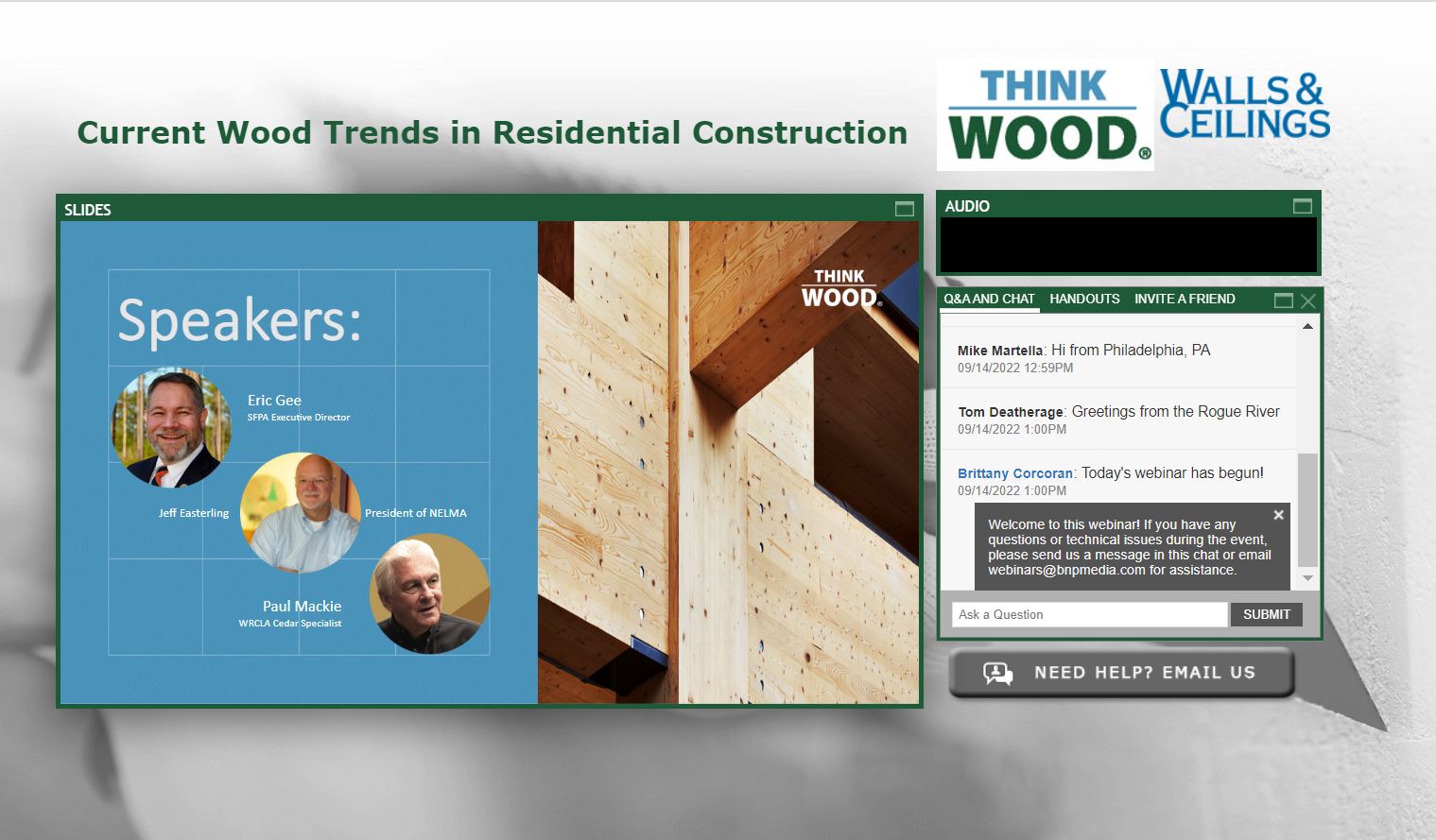
Think Wood has been continuing to contribute to the conversation around the benefits of wood construction—sustainable and otherwise—through a series of media integrations with industry publications. These partnerships—which take the form of webinars, articles, research, CEU courses, and more—allow Think Wood to engage with its target audiences of architects and developers and to provide thought leadership content that shows them how building with wood can be beneficial on future projects.
The most successful media integration of Q3 was a webinar with Architectural Record called “The Future Is Factory Built,” which considered how prefabricated wood systems can help speed construction. That webinar netted Think Wood nearly 450 new architect and developer contacts, and resulted in more than 500 downloads of educational resources produced by Think Wood. Integrations with The Architect’s Newspaper through its Facades+ and TimberCon events netted an additional nearly 350 new contacts. And partnerships with Multifamily Executive’s Concept Community and Wealth Management Real Estate’s annual research on the multifamily market led to more than 1,000 engagements to build awareness about the benefits of wood products with the difficult-to-reach developer audience.
This year, Think Wood also started a push to reach more residential contractors, with a focus on thought leadership to help contractors understand the benefits of continuing to use wood for decking and finish applications—in addition to structure—even as more material alternatives come to market. A webinar with Walls & Ceilings—led by Eric Gee of the Southern Forest Products Association, Jeff Easterling of the Northeastern Lumber Manufacturers Association, and Paul Mackie of the Western Red Cedar Lumber Association—walked nearly 150 residential contractors through the various species of softwood and the best applications for each. That webinar will stay online, viewable on demand, for a full year, continuing to increase Think Wood’s reach with that audience.
By expanding outreach and nurturing more connections in the architect, developer, and residential contractor spaces, Think Wood is helping to encourage the AEC industry to understand that wood products can help to build a more sustainable built environment today, fostering the use of more wood in projects.
WoodWorks Lays Groundwork for Sound LCA Practices
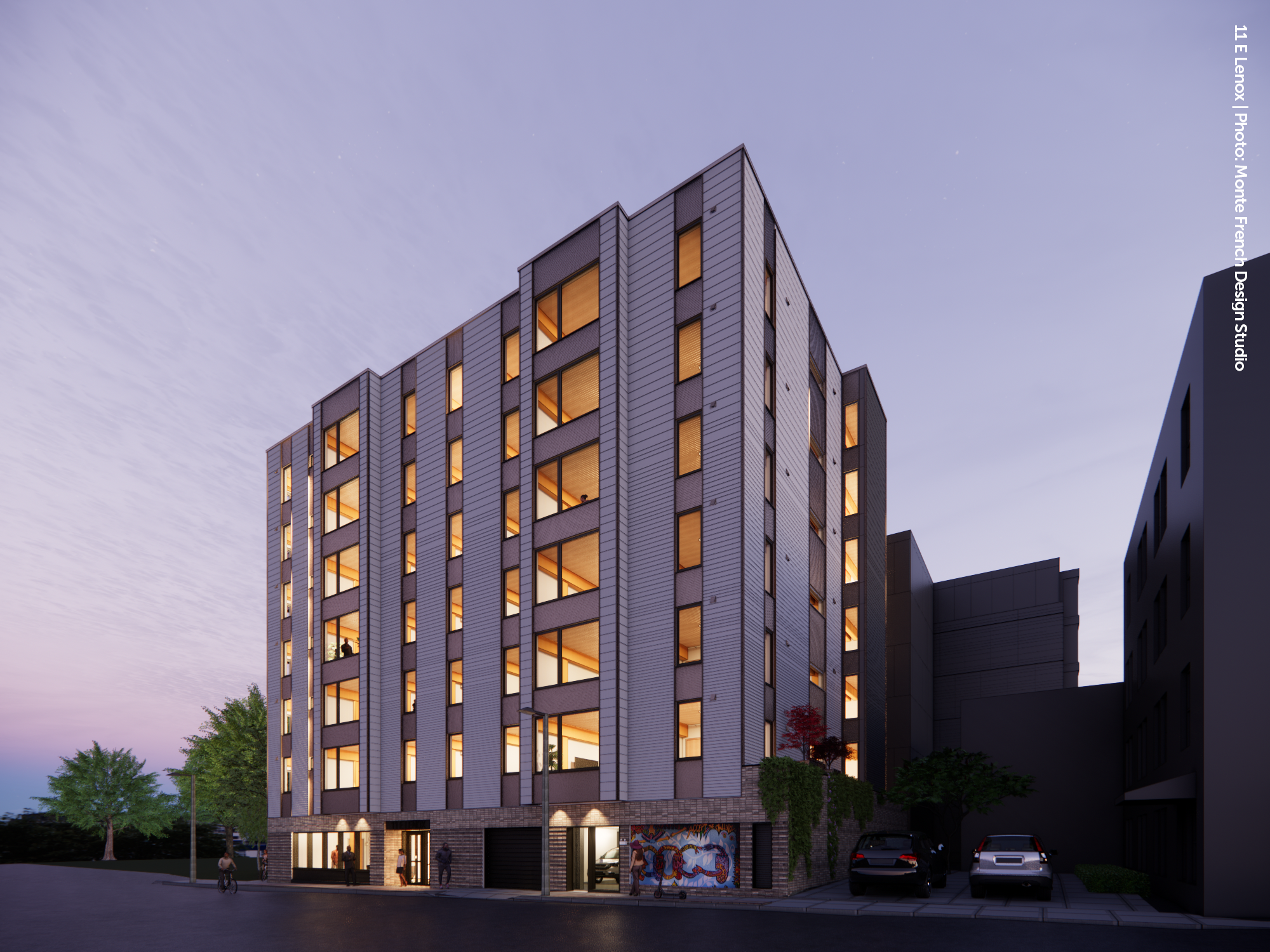
While wood products should be seen as the go-to solution for mitigating climate change, other material industry groups have been attempting to shift discussion of carbon impact in directions they favor. After working with the AWC and Think Wood to define roles, identify key priorities, and lay the groundwork for coming efforts, WoodWorks has recently taken several tangible steps to emphasize sound building science.
To support the design and construction community with relevant and transparent information on wood’s environmental performance, WoodWorks published the following expert tips:
• Introduction to Whole Building Life Cycle Assessment: The Basics
• When to Include Biogenic Carbon in an LCA
• Current EPDs for Wood Products
• Calculating the Carbon Stored in Wood Products
The program has also been working with Haycon, the contractor for 11 E. Lenox, a tall mass timber building in Boston. Haycon specializes in passive house design and high-energy-efficiency structures and wants to expand its focus to the embodied carbon benefits of mass timber. WoodWorks funded the design of an equivalent steel-framed structure with concrete-on-metal deck floors and a life cycle assessment (LCA) study to compare the design with the as-built structure using the Athena Impact Estimator. The report has yet to be finalized, but initial results are promising.
Through its work, WoodWorks has realized how challenging it is for project teams to create accurate material take-offs because of inconsistencies in modeling, different levels of detail between as-built and alternative designs, and a lack of expertise in cost and material estimating among team members. Based on this finding, WoodWorks intends to further investigate how design teams approach material estimation and to provide the teams guidance and rules of thumb. The intended result: more accurate studies that convey the full carbon benefits of wood construction.
Industry News
Maine’s First Mass Timber Office Building Will Promote CLT Adoption

Developers hope a new mass timber commercial office building, the first of its kind in the state of Maine, will help fuel commercial adoption of CLT and support the attraction of a CLT manufacturer to the state. The 150,000-square-foot building at 100 Rock Row in Westbrook will be funded in part by a $250,000 grant from the USDA Forest Service’s Wood Innovations Grants program.
Developer Waterstone Properties Group believes “this project will promote the economic future of Maine’s timber industry and environmental health of communities by helping to establish the market for a regenerative and sustainable building material that also has a tremendous impact on the health and wellness of employees,” Waterstone principal Josh Levy said in a news release.
Designed by EYP, a Page Co., an architecture firm out of Albany, New York, 100 Rock Row will include 30,000 square feet of retail space on the first floor. It joins the larger Rock Row development that, once completed, is expected to attract six million visitors a year and employ more than 4,000 people.
Learn more about the project here.
Why Increased Focus on Embodied Emissions is an ‘Ironclad Rule of Carbon’
Environmentally conscious architects and designers have long focused their sustainability efforts on improving energy efficiency and reducing carbon emissions from building operations. But as designers have made progress on those efficiency goals and the energy supply has become cleaner, that calculation has changed: It takes longer for the cumulative operating energy of a highly efficient building to overtake the embodied energy of the materials used in the building’s construction.
In his Treehugger blog, Lloyd Alter, a lecturer in sustainable design at Toronto Metropolitan University’s School of Interior Design at The Creative School, describes the concept as the “ironclad rule of carbon” that applies not just to buildings, but to everything: “As more of our stuff, from cars to tools, run on electricity, as our electrical grids get cleaner, as our building efficiencies get better, then the issues of embodied or upfront carbon become more important.”
Alter argues that designers can’t ignore a building’s upfront emissions, and prioritizing low- and zero-carbon materials—such as wood—is one of the key tenets of that approach.
Read Alter’s blog here.
‘Architecture at Home’ Exhibit Has Five Prototype Homes That Show Housing Can Be ‘Sustainable and Attainable’
Housed at the Crystal Bridges Museum of American Art in Bentonville, Arkansas, “Architecture at Home” is an exhibition that offers solutions to the dwindling stock of financially accessible housing. The institution engaged five architecture firms—studioSUMO from New York and Los Angeles, LEVENBETTS from New York, Mutuo from Los Angeles, Pérez Palacios Aquatints Asociados from Mexico City, and studio:indigenous from Wisconsin—to design a house for a family of three that would cost less than $200,000. And while one aspect of the show is the fully developed build-ready plans for a house by each firm, many of which included wood products, “what we’re doing is not giving solutions for the exact model of a house you would build,” curator Dylan Turk told Fast Company, “but a new way of talking about the problem, a new way of approaching changing how we live, that starts from the human side with a human-focused design, rather [than] from a number, data-driven side.”
To that end, each team constructed a pavilion on the museum’s grounds that explores concepts that the architects envision changing both the design and accessibility of housing. To explore the opportunities and barriers to sustainable material sourcing and regulation, the prototype by LEVENBETTS is a timber house annotated with details about the lumber supply chain that brought the materials to the site and the rules regulating timber construction.
See the other prototypes and read the article here.
Massachusetts Mass Timber Project Targets Passive House Standards
A new multifamily active-adult community in Northampton, Massachusetts, will have a structure built completely from mass timber. Designed by BKSK Architects and developed by Live Give Play and Spiritos Properties, LLC, the project is also targeting the ambitious Passive House energy efficiency standard with rooftop solar and a highly efficient building envelope.
“We are committed to delivering a building that showcases best practices for the construction industry, which has struggled to meet the moment of impending climate crisis,” said Jeff Spiritos of Spiritos Properties in Construction Specifier. “By building to a carbon-negative, net-zero ready design, we’re proving how mass timber construction and Passive House certified standards are not only viable options for all multistory buildings including rental housing, but they are also its future.”
The design makes the most of timber’s warm beauty on the interior by partially exposing the building’s wood columns, beams, and ceilings—which will also reduce the use of paints and other artificial finishes. Spiritos Properties specializes in mass timber and tall wood buildings and was selected as one of the two winners of the USDA- and SLB-sponsored U.S. Tall Wood Building Prize Competition in 2015.
Read more about the project here.
The Disappearing Starter Home—and What Might Replace It
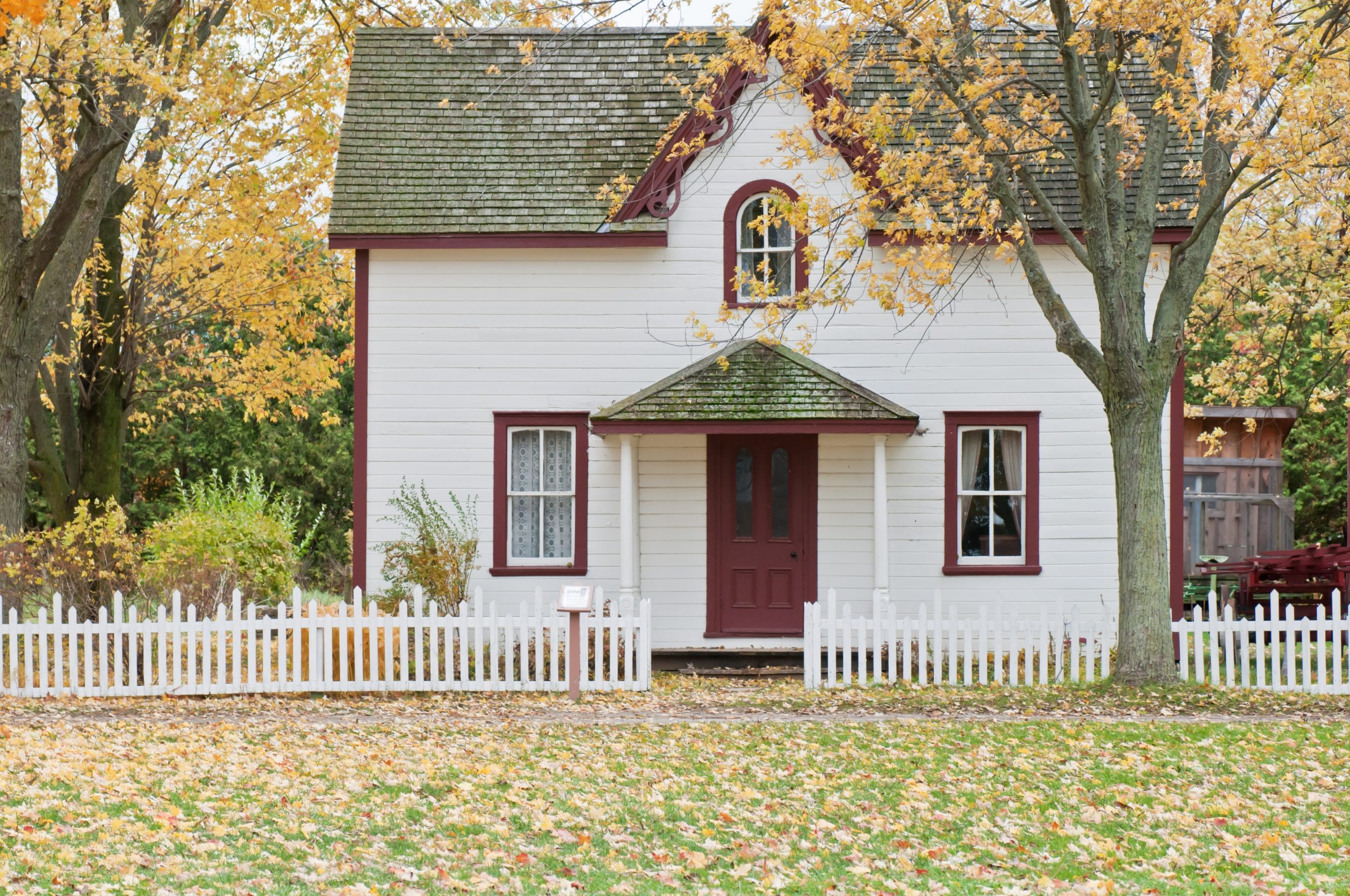
Whatever happened to the starter home? In an article for The New York Times, Emily Badger investigates the disappearing entry-level home market.
“The affordable end of the market has been squeezed from every side,” she writes. “Land costs have risen steeply in booming parts of the country. Construction materials and government fees have become more expensive. And communities nationwide are far more prescriptive today than decades ago about what housing should look like and how big it must be. Some ban vinyl siding. Others require two-car garages. Nearly all make it difficult to build the kind of home that could sell for $200,000 today.”
As a result of this confluence of factors, builders have virtually ceased to construct small detached homes. According to CoreLogic, nearly 70% of new houses in the 1940s were 1,400 square feet or less. Today, that figure is 8%. With little relief from demographic shifts or rising land costs on the horizon, some buyers and communities are looking at condos and housing types such as triplexes and fourplexes as potential solutions. But with code and zoning changes, some developers feel that there could be opportunity to build more homes at the more affordable, and in-demand, end of the market.
Read the article here.
Insights on the Competition
Hydrogen-Fueled Production Could Decarbonize the Steel Industry
Virtually every manufacturing sector is seeking ways to position its products in the effort to decarbonize our economy, and steel manufacturing is no exception. The latest hope in the effort to produce “greener” steel is hydrogen. In a new infographic, the Visual Capitalist blog takes a look at the opportunities and challenges for using hydrogen to decarbonize steel manufacturing.
Steel is traditionally manufactured using coke, a high-carbon, coal-based fuel. Green steel production uses hydrogen to turn iron pellets into sponge iron, which can be processed to form steel at lower temperatures, cutting energy costs. But producing enough hydrogen to meet global demand for steel, and especially doing so in an environmentally friendly way, remains a challenge. Green hydrogen production costs are currently higher than traditional fossil fuel methods. Some steel manufacturers are piloting green steel production facilities, however, with seven projects in the works in Germany alone.
Check out the infographic here.
Industry Resources
FEA’s Housing Dashboard
Virginia Tech's Monthly Housing Report
This monthly housing commentary report is a free service of Virginia Tech and is intended to help one gauge future business activity in the U.S. housing market.
August 2022 Reports (released in October 2022)
Part A: August Housing Commentary
Part B: August Economic Conditions