HIGHLIGHTS
PROGRAM UPDATES
WoodWorks Engages Developers on Mass Timber at ULI’s Spring Meeting The American Wood Council Works to Prevent Unnecessary Changes to Plumbing and Mechanical Codes The AWC Prioritizes Outreach to Engineers Think Wood Profiles Wood’s Role in Low-Carbon Passive House Buildings The SLB and Clemson Team to Host New Timber Design Workshop for FacultyINDUSTRY NEWS
New York City’s First Mass Timber Condo Building Nears Completion Wood Decks, Other Exterior Improvements Offer Best ROI to Homeowners Northeastern Lumber Manufacturers Association Launches Integrated Website to Better Serve Its Diverse Audiences Chemically Engineered, Recycled Wood Rivals Steel’s StrengthINSIGHTS ON THE COMPETITION
The Latest on Concrete’s Push to Lower EmissionsProgram Updates
WoodWorks Engages Developers on Mass Timber at ULI’s Spring Meeting
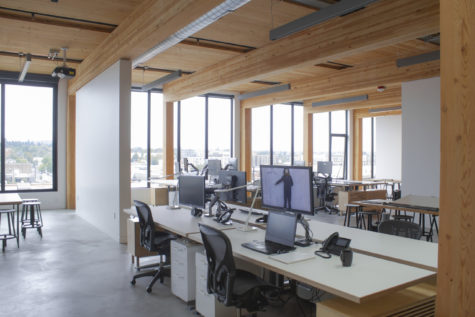
WoodWorks enjoyed significant attention at the Urban Land Institute’s (ULI) spring meeting in San Diego, which engaged more than 4,400 cross-disciplinary real estate and land-use experts in discussions about the built environment. As part of the meeting, WoodWorks hosted two sessions on mass timber construction for over 300 developers and investors.
In “Business Case: Real Numbers on Real Mass Timber Deals,” WoodWorks introduced the session and drew attention to three new mass timber case studies of interest—the six-story District Office building in Portland, Oregon; the four-story 1 De Haro office building in Sacramento, California; and Adohi Hall, a 202,491-square-foot on-campus housing project at the University of Arkansas. WoodWorks’ current business case study package, which contains seven mass timber projects, is available on WoodWorks’ website.
In “Mass Timber: Contributing to Wildfire Resilience and Financial Returns,” WoodWorks discussed the connection between mass timber and wildfire resilience with Paul Hessburg, Research Landscape Ecologist with the U.S. Forest Service, and Paul Stein, Managing Partner at SKS Partners, the developer of 1 De Haro. Stein credits mass timber with helping to advance and secure financing for 1 De Haro, ultimately achieving California’s first large-scale, speculative office building constructed with CLT. GlobeSt.com, a commercial real estate publication, covered this session in “Mass Timber a Key Material for ESG-Driven Tenants.”
Photo credit: District Office, Hacker
The American Wood Council Works to Prevent Unnecessary Changes to Plumbing and Mechanical Codes
At a recent International Association of Plumbing and Mechanical Officials’ technical hearings, the American Wood Council (AWC) submitted public comments and testified against two proposed changes to the 2024 Uniform Plumbing and Mechanical Codes that would unnecessarily hinder mass timber construction. The changes sought to limit the use of plastic piping in mass timber construction and to add a requirement for the engineered design of plumbing and mechanical systems; both changes would have resulted in increased costs for mass timber building construction.
The AWC’s efforts were successful in that both proposals were amended to remove restrictions on the use of plastic piping in all mass timber buildings, thereby eliminating the threat to the softwood lumber industry. Both proposals will next be voted on at the association’s Technical Committee Convention in September. The AWC will continue to track both proposals and look out for others that may carry an intended or unintended consequence of increasing the cost of mass timber construction.
The AWC Prioritizes Outreach to Engineers
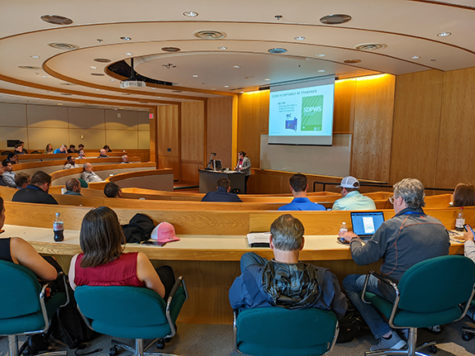
Lori Koch, the AWC’s director of educational outreach and a structural engineer by training, recently presented updates to the 2021 Special Design Provisions for Wind and Seismic to over 120 engineers at the Oklahoma Structural Engineers Association’s annual meeting. The session covered the SDPWS’s new provisions for the design of CLT diaphragms and shear walls and included a lively Q&A session, during which Koch and participating engineers discussed the justification for design value changes, the use of alternative fastenings, domestic CLT production, and implementing CLT assemblies.
Maintaining relationships with state Structural Engineers Association chapters is an ongoing priority for the AWC and is an effective means to share the latest versions of AWC standards directly with engineers from firms of varying sizes.
Think Wood Profiles Wood’s Role in Low-Carbon Passive House Buildings

Think Wood recently spoke with Ruth Mandl and Bobby Johnston, co-principals of Brooklyn-based CO Adaptive Architecture, about lessons learned from past low-carbon projects and their vision for how low-carbon construction might evolve. Mandl and Johnston’s practice explores how modularized and prefabricated mass timber assemblies, built to Passive House standards, can be used in urban, adaptive reuse projects.
Passive House is a building standard that was developed in Germany in the early 1990s. It focuses on high-performance construction using extensive insulation, energy-efficient windows, and an airtight membrane that wraps entire structures, reducing the impacts of hot and cold weather. When done right, all these factors can combine to reduce the operational energy consumption of a building by 80 to 90%, resulting in reduced emissions and significant energy savings.
According to Mandl, prefabricated timber systems can play an important role in Passive House design. Thermally, wood is superior to steel and offers added thermal mass. All CO Adaptive’s Passive House projects use wood as the primary material. Wood provides more versatility and, given its natural renewability, lends itself to CO Adaptive’s goals of regenerative, circular design.
“Cutting embodied and operational energy is . . . part of a regenerative approach to sustainability,” stated Mandl. “To do this, it makes sense to use low-carbon building materials—like timber—and design for disassembly with adaptability in mind, so that things can be taken apart, reused, and become part of a circular design loop.”
Learn about one of CO Adaptive’s most recent timber projects here.
The SLB and Clemson Team to Host New Timber Design Workshop for Faculty
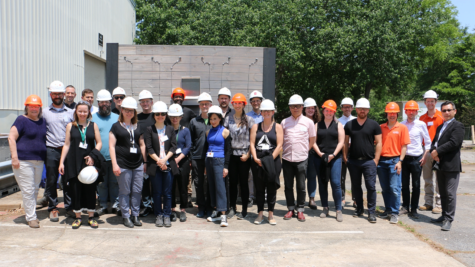
In May, the SLB and Clemson University’s School of Architecture and Wood Utilization + Design Institute (WU+D) partnered to host a first-ever, four-day, hands-on workshop to educate architecture faculty on mass timber design and building and to discuss strategies for incorporating mass timber into their programming. The workshop featured six interactive sessions on design, cross-disciplinary research and collaborations, curricular frameworks, funding, and sourcing; tours of Clemson’s mass timber facilities; and presentations from eight guest speakers with expertise in building successful, university-level timber design programs. Twenty faculty members from 18 institutions were selected to participate.
In speaking at the workshop’s conclusion, Dustin Albright, Associate Professor and Assistant Director of Clemson’s School of Architecture, noted, “The workshop provided a really great opportunity for diverse faculty from diverse architecture programs across the country to get together and discuss common themes and interests relating to timber design. . . . I know that I learned a lot, and I expect the same is true for everyone who attended.”
The success of the workshop has provided a repeatable model for energizing and supporting faculty to teach material studies and wood design in schools that are doing so today. SLB Education expects to fund additional similar workshops in 2022 and beyond.
Read more about the workshop here.
Industry News
New York City’s First Mass Timber Condo Building Nears Completion
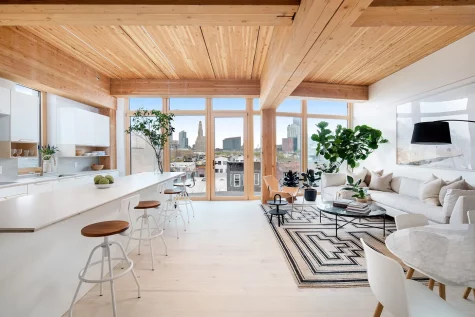
Construction of the six-story, mass timber 670 Union multifamily project is nearing completion in New York City’s Park Slope neighborhood. Designed by Mesh Architectures and developed by Brooklyn Home Company, the building will be New York City’s first mass timber condominium. It is also built to Passive House standards.
The project represents an important milestone in advancing mass timber construction—and overall green building construction—in New York City. City officials have been slowly warming to mass timber for the past decade and only included CLT for buildings up to 85 feet tall in their 2022 codes. Appreciating this operating context, the Mesh team was proactive in engaging building and code officials early in the project’s design, and it pivoted from the desired CLT to glulam to ultimately win project approval. By leveraging prefabrication technology, the project went up more quickly than a conventional build.
Read more about the project here.
Wood Decks, Other Exterior Improvements Offer Best ROI to Homeowners
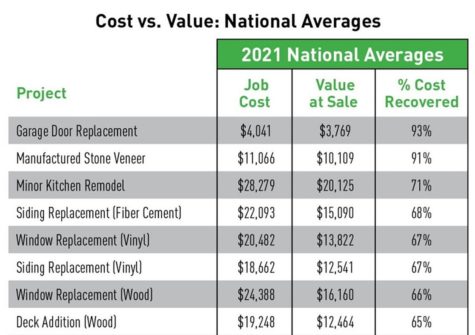
According to Zonda’s 2022 Cost vs. Value Report, exterior home improvement projects continue to provide the greatest return on investment to homeowners despite elevated material and labor costs. The report tracks the year-over-year ratio of value over cost for 22 types of common remodeling projects, 11 of which are exterior replacement projects. In the 2022 report (which summarizes 2021 activity), all 11 exterior project types—including wood decking and wood window replacement—ranked among the top 12 projects with the highest ROI. Composite decks delivered a lower return on investment than wood ones due to job cost.
Report authors note that although ROI values have been trending upward for the past five years, overall growth in returns has been hampered by rising material costs since 2014 and particularly over the last two years. This is true for wood deck replacement, whose ROI has charted a serpentine curve since 2014 because of higher material costs. Fortunately, irrespective of rising costs and supply chain challenges, overall cost versus value trends suggest that the repair and remodeling market is resilient.
While still returning a decent ROI, larger discretionary projects and high-end room editions, such as master-suite additions, generally have a lower impact on home pricing and, thus, ROI.
Read more about the 2022 Cost vs. Value Report, and access the data here.
Northeastern Lumber Manufacturers Association Launches Integrated Website to Better Serve Its Diverse Audiences
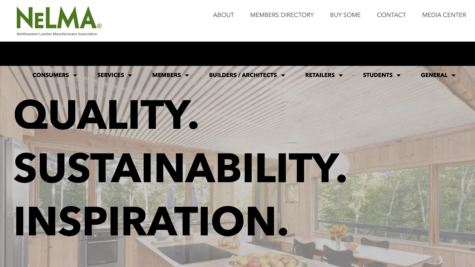
The Northeastern Lumber Manufacturers Association (NELMA) recently launched a redesigned website, NELMA.org, as a one-stop shop for its diverse audiences to access information regarding NELMA’s products and programs. According to Jeff Easterling, NELMA’s President, “We’re bucking the old trend of vanity websites for separate products and programs. . . . Retailers need to know product information that helps them sell more wood easily and clearly; consumers want instant inspiration; builders and contractors need help from one source; and architects don’t want to search and hop around the internet. With the new NELMA.org, it’s all in one place in a clearer, cleaner, more educational format.”
Learn more about NELMA’s web redesign here, and visit the site today.
Chemically Engineered, Recycled Wood Rivals Steel’s Strength
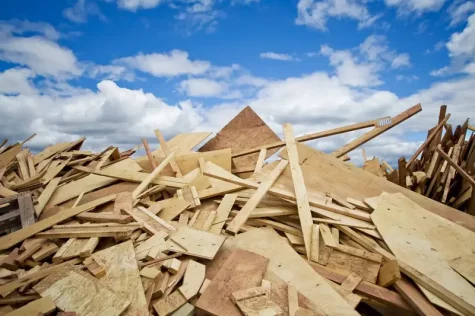
A team of researchers led by Orlando Rojas, the Scientific Director of the Bioproducts Institute at the University of British Columbia, has developed a process to chemically recycle waste wood in order to produce a material that is stronger than steel. Known as “healed wood,” the material, which can be created from any timber byproduct, including sawdust, is also five times stronger than natural wood.
The process uses a common cellulose solvent to treat the old wood and then binds two pieces of treated wood together to create the new material. Testing shows that the healed wood is more resistant to breaking than titanium alloys and stainless steel.
Rojas and his team did not examine how much their method would cost if scaled up to an industrial level; however, according to Rojas, “The processes that we use here are very typical in wood processing . . . so scalability is not an issue.” Scaling up would enable greater wood reuse, thereby diverting tons of waste wood from landfills.
Read more about the technology here.
Insights on the Competition
The Latest on Concrete’s Push to Lower Emissions
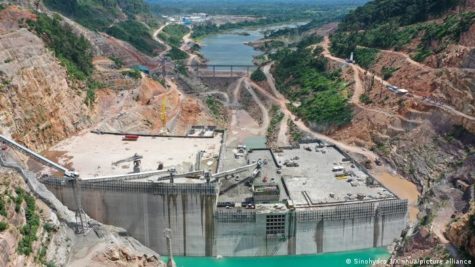
The concrete and cement industry is a prolific producer of carbon dioxide emissions, accounting for 8% of global emissions. German international broadcaster Deutsche Welle (DW) recently reviewed the concrete industry’s efforts to come up with new technologies and processes to create less carbon-intensive materials and fully decarbonize by 2050.
DW notes that the industry plan to decarbonize—which was put forward in 2021 by the Global Cement and Concrete Association (GCCA)—relies on producing cement and concrete more efficiently, designing more efficient and durable buildings (over which the concrete industry itself has little control), and capturing carbon dioxide after it has been released, which to date has been untested at scale. Regarding this final point, DW contends, “That means a cornerstone of the industry’s plans rests on a technology that isn’t yet ready to fix the problem.”
DW notes that GCCA is working to apply carbon-capture technology at an industrial scale in 10 cement plants by 2030, including at a German-built plant in Norway. In the meantime, some smaller-scale solutions are emerging, including a Swedish pilot project that shows how cement can be produced using energy generated from sources other than fossil fuels and a French effort to convert “cement bypass dust into lightweight aggregates using CO2 captured on-site.” The cost associated with these carbon-capture processes poses a significant barrier to widespread uptake.
DW also notes that “concrete’s carbon footprint could also be lowered by using sustainably sourced timber in construction,” though this would potentially create unsustainable pressure on forest resources. [Editor’s Note: DW’s statement runs contrary to industry research, summarized here.]
Read more from DW here.
Industry Resources
FEA’s Housing Dashboard
This housing dashboard is provided compliments of Forest Economic Advisors (FEA). View the May Dashboard
Virginia Tech's Monthly Housing Report
This monthly housing commentary report is a free service of Virginia Tech and is intended to help one gauge future business activity in the U.S. housing market.
April 2022 Reports (released in June 2022)
Part A: April Housing Commentary
Part B: April Economic Conditions